Business Growth Through Innovation in Injection Moulding
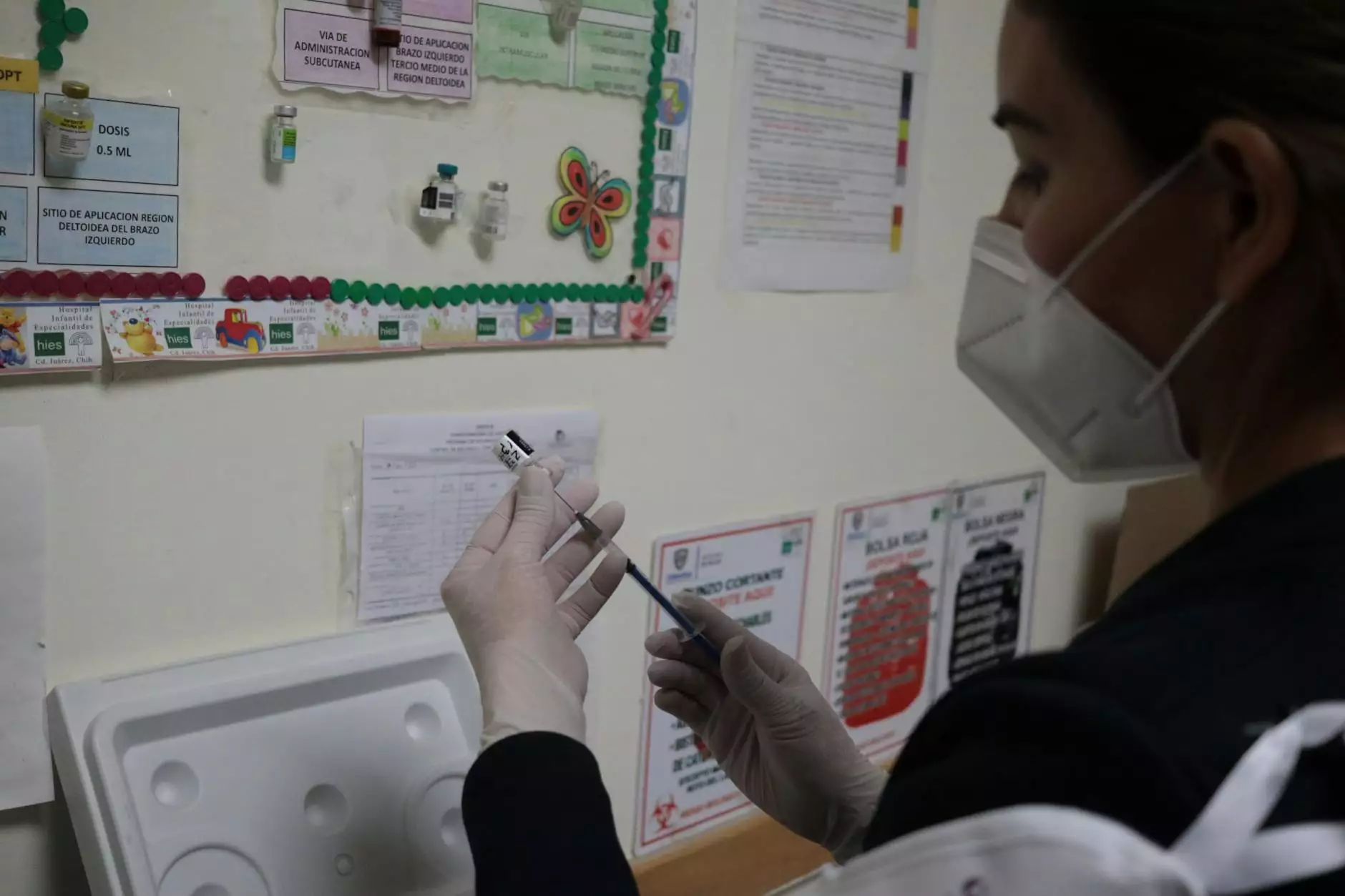
Understanding Injection Moulding
Injection moulding is a manufacturing process that processes molten material into desired shapes through a mold. It plays a critical role in various industries, especially in the production of precision components for electronic devices and medical supplies. With the rise of technology, the demand for high-quality moulded parts continues to increase.
The Importance of Choosing the Right Supplier
When selecting an injection moulding supplier, businesses must consider factors such as experience, technical capabilities, and quality control standards. A strategic partnership with the right supplier, like Nolato, can lead to enhanced product performance and operational efficiency.
Why Choose Nolato as Your Injection Moulding Supplier for Xilinx
Nolato has established itself as a reliable injection moulding supplier for Xilinx, offering a range of specialized services tailored for both the electronics and medical supplies industries. Here are some compelling reasons to partner with Nolato:
- State-of-the-Art Technology: Our facilities are equipped with the latest injection moulding machines and technology, ensuring precise moulding processes.
- Expertise in Electronics & Medical Supplies: With extensive experience in these sectors, we understand the unique requirements involved.
- Quality Assurance: We adhere to strict quality control protocols, guaranteeing that every product exceeds industry standards.
- Sustainability: Nolato is committed to sustainable manufacturing practices, minimizing environmental impact while maximizing efficiency.
- Customized Solutions: We offer flexible solutions tailored to meet specific client needs, promoting better alignment with your operational goals.
The Process of Injection Moulding
The injection moulding process consists of several critical stages, each of which contributes to the overall quality of the finished product:
- Material Preparation: Selecting the right material mix is crucial. We utilize high-grade thermoplastics and elastomers to guarantee durability and performance.
- Mould Design: Our engineering team collaborates with clients to design custom moulds that perfectly meet their specifications.
- Injection: The molten material is injected into the mould cavity at high pressure, ensuring it fills every nook and cranny.
- Cooling: Once injected, the material is cooled to solidify, forming the final product.
- Demoulding: The finished piece is removed from the mould, ready for final inspection and delivery.
Nolato's Commitment to Quality Control
At Nolato, we understand that quality is non-negotiable when it comes to components used in electronics and medical applications. Our comprehensive quality control measures include:
- In-Process Quality Checks: Ongoing monitoring during production ensures each step meets our rigorous standards.
- Final Inspection: Every product undergoes thorough inspections, confirming adherence to specifications and regulations.
- Certification and Compliance: We maintain compliance with industry certifications, including ISO 9001, ensuring our processes meet global benchmarks.
- Customer Feedback: We actively seek and incorporate client feedback, continuously improving our processes and products.
Innovative Applications of Injection Moulding in Electronics
The electronics industry relies heavily on injection moulding for producing various components. Let’s explore some cutting-edge applications:
- Circuit Board Enclosures: Custom moulded enclosures protect delicate circuit boards from damage and offer aesthetic appeal.
- Connectors and Adaptors: Precision moulding enables the creation of intricate shapes for connectors that ensure secure connections.
- Sensor Housings: With the growth of IoT, sensor housings made from durable moulded plastics help facilitate various smart technologies.
- Heat Sinks: Moulded heat sinks effectively dissipate heat in electronic devices, enhancing their reliability and performance.
Injection Moulding in Medical Supplies
In the medical field, injection moulding is vital for producing components that are not only functional but also safe for human use. Key applications include:
- Surgical Instruments: Custom-moulded surgical instruments cater to unique designs that improve usability.
- Disposable Devices: High-volume production of single-use devices ensures sterility and minimizes infection risks.
- Medical Packaging: Moulded packaging solutions protect sensitive medical components while ensuring compliance with health regulations.
- Implants and Prosthetics: Tailor-made moulds are used to create implants that fit patient specifications perfectly, improving overall effectiveness.
Future Trends in Injection Moulding
As technology evolves, so does the landscape of injection moulding. Some trends to watch include:
- Advanced Materials: The introduction of composite materials will enhance the capabilities of injection moulded products.
- Smart Manufacturing: The integration of IoT technology can lead to more efficient production systems and predictive maintenance.
- Sustainability Initiatives: There will be an increased focus on eco-friendly practices, including recycling and biodegradable materials.
- Automation: Enhanced automation technology will improve precision and reduce cycle times, leading to greater efficiency.
Partnering with Nolato for Success
In summary, choosing Nolato as your injection moulding supplier for Xilinx can be a game-changer for your business. Our commitment to quality, innovation, and customer satisfaction positions us as a leader in injection moulding.
If you're looking to streamline your manufacturing processes while producing high-quality components for electronics or medical supplies, look no further than Nolato. Connect with us today to find out how we can help your business succeed through innovative solutions in injection moulding!
Contact Us
Ready to elevate your business with top-notch injection moulding services? Contact Nolato now!
injection moulding supplier xilinx